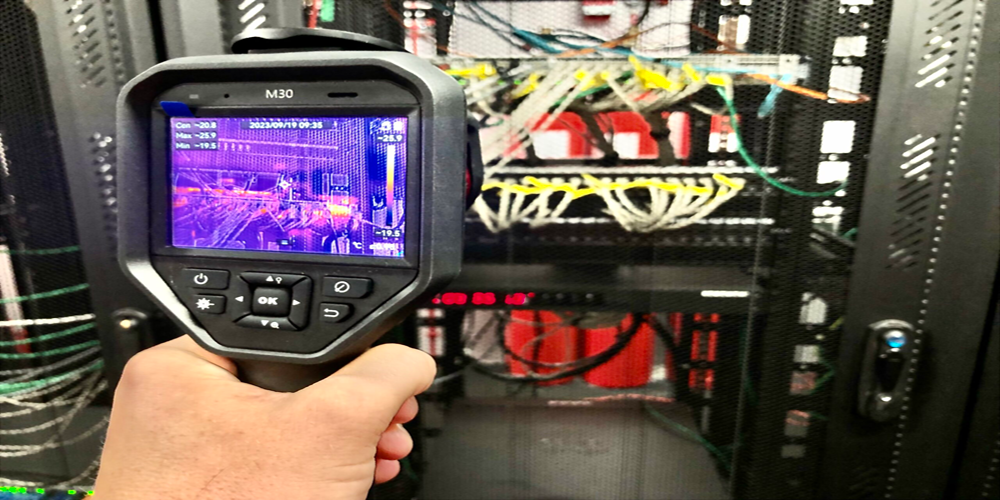
Exploring the Power of Electrical Thermal Imaging Inspections
Electrical systems are the backbone of modern infrastructure, powering industries, homes, and businesses alike. However, with great power comes great responsibility. Electrical faults, failures, and inefficiencies can lead to devastating consequences, including fires, equipment damage, and even loss of life. To mitigate these risks, electrical thermal imaging inspections have emerged as a powerful tool in the maintenance and troubleshooting of electrical systems.
In this guide, we’ll delve into the principles, applications, benefits, and best practices of electrical thermal imaging inspections, shedding light on how they enhance safety and efficiency across various sectors.
Understanding Thermal Imaging Inspections
Thermal imaging, also known as thermography, is a non-destructive testing technique that visualizes temperature variations across an object or surface. It relies on the principle that all objects emit infrared radiation based on their temperature. By detecting and measuring this radiation, thermal cameras create detailed images called thermograms, where different temperatures are represented by varying colors or shades.
In electrical systems, thermal imaging inspections involve capturing thermographic images of components such as wires, connections, switches, and circuit breakers. These images reveal temperature anomalies that may indicate potential issues such as loose connections, overloaded circuits, unbalanced loads, or equipment malfunction. By identifying these anomalies early, maintenance teams can take proactive measures to address them before they escalate into serious problems.
Applications of Electrical Thermal Imaging Inspections
The applications of electrical thermal imaging inspections span across various industries and sectors:
Preventive Maintenance: Thermal imaging inspections enable proactive identification of hot spots and potential failures in electrical equipment, allowing maintenance teams to schedule repairs or replacements before costly downtime occurs.
Electrical Distribution Systems: Thermal imaging is widely used to inspect switchgear, transformers, distribution panels, and other components of electrical distribution systems in industrial facilities, commercial buildings, and utility substations.
Building Inspections: In commercial and residential buildings, thermal imaging helps detect overheating in electrical wiring, outlets, and electrical appliances, reducing the risk of electrical fires and enhancing overall safety.
Renewable Energy: Thermal imaging is valuable in the inspection of solar panels, wind turbines, and other renewable energy systems, ensuring optimal performance and early detection of potential faults.
Manufacturing: Electrical thermal imaging is utilized in manufacturing environments to monitor the condition of machinery, control panels, and electrical infrastructure, minimizing the risk of production disruptions and equipment downtime.
Benefits of Electrical Thermal Imaging Inspections
The adoption of electrical thermal imaging inspections offers numerous benefits:
Early Detection of Faults: Thermal imaging enables early detection of overheating components, allowing for timely intervention and prevention of equipment damage or failure.
Improved Safety: By identifying potential fire hazards and electrical faults, thermal imaging inspections contribute to a safer work environment for personnel and occupants.
Increased Efficiency: Proactive maintenance based on thermal imaging findings minimizes unplanned downtime, improves equipment reliability, and extends the lifespan of electrical assets.
Cost Savings: Preventive maintenance reduces repair costs, equipment replacement expenses, and losses associated with downtime, ultimately resulting in significant cost savings for organizations.
Compliance and Insurance: Regular thermal imaging inspections help businesses comply with industry regulations and insurance requirements, demonstrating a commitment to safety and risk management.
Best Practices for Electrical Thermal Imaging Inspections
To maximize the effectiveness of thermal imaging inspections, adhere to the following best practices:
Qualified Personnel: Ensure that thermal imaging inspections are conducted by certified thermographers with relevant training and expertise in electrical systems.
Proper Equipment: Use high-quality thermal cameras calibrated for electrical inspections, capable of capturing accurate temperature measurements and detailed thermographic images.
Comprehensive Inspection Plans: Develop thorough inspection protocols specifying the components to be inspected, inspection frequencies, and evaluation criteria for temperature anomalies.
Safety Precautions: Adhere to safety protocols, including de-energizing equipment when possible, wearing appropriate personal protective equipment (PPE), and following established lockout/tagout procedures.
Documentation and Reporting: Maintain detailed records of inspection findings, including thermograms, temperature measurements, and recommendations for corrective actions. Provide clear and concise reports to stakeholders, highlighting identified issues and proposed solutions.
Regular Monitoring: Implement a regular inspection schedule to monitor changes in temperature patterns over time, enabling early detection of emerging issues and trend analysis.
Looking at Electrical Thermal Imaging Inspections
Electrical thermal imaging inspections have revolutionised the way we assess and maintain electrical systems, offering a proactive approach to safety, reliability, and efficiency. By leveraging thermal imaging technology, organisations can detect potential faults, mitigate risks, and optimise the performance of their electrical infrastructure.
As industries continue to prioritize safety and reliability, thermal imaging inspections will remain indispensable tools in the maintenance toolkit, ensuring the smooth operation of electrical systems in a wide range of applications.